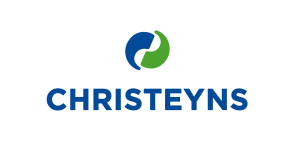
6 October 2021
In a joint venure with engineering company Veride, hygiene chemical specialist Christeyns launches HydRO, a new technology to help professional laundries reduce fresh water consumption.
With growing awareness and responsibility around water use and water quality and stricter effluent regulations coming into force in several European countries, water and wastewater management practices are of the upmost importance in the commerical laundry sector. HydRO technology is expected to play a vital role in decreasing the environmental impact of industrial washing and contribute in lower water-related costs for customers.
Typically four to ten litres of water are used per kg linen in an industrial laundry setting, HydRO can reduce fresh water consumption by at least 80%. In combination with effective rainwater collection, the technology enables the reduction of fresh water consumption to only 0.5 litre per kg of linen.
“Empowering our customers to massively reduce their water consumption and effluent bills, to save energy and reduce their CO2 impact significantly, that’s what this partnership with Veride is all about,” comments Alain Bostoen, CEO Christeyns.
The joint venture offers a modular system for water recovery, treatment and recycling, collecting polluted streams of wastewater from the washhouse to purify and reuse it. In short, a closed-loop water supply reclaiming at least 80% of the process water and transforming it into fresh water with all substances such as micro-plastics, heavy metals and bacteria filtered out.
“As water recycling presents a huge opportunity for the laundry industry, we need to redefine water management for sustainable growth. We look forward to offering our customers this new technology which will have a positive impact across all aspects of their business,” adds Christeyns UK Engineering Manager Peter Jackson.
This water-saving system is a plug-and-play solution delivered in container units customised to target wastewater quantity. The HydRO technology makes all additional treatment such as iron removal, softening, reverse osmosis and wastewater treatment obsolete. In addition, a heat-exchanger is no longer required as the reclaimed water has a temperature of 40°C.
HydRO will be the latest addition to Christeyns’ Engineering portfolio, driving innovation in the laundry arena across the UK and Ireland. Veride and Christeyns co-own the brand, each having a 50% stake. The HydRO technology has already been implemented in over 10 industrial laundries in the BeNeLux with great success and will now be available in the UK.
For further information visit: