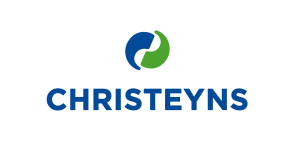
23 December 2021
Christeyns, who manufacture and supply detergents and supporting chemicals for the UK laundry sector, has recently taken on four new apprentices.
Isabel Hardwick has joined the firm as Apprentice Quality Control Technician following success in her A level examinations. Izzy’s apprenticeship will last four years and incorporates working towards a BSc (Honours) in Chemistry at Bradford University.
Danny Clarke and Tom Grundell have both taken up two-year apprenticeships as HGV Drivers. During this time, they will study to obtain an NVQ Level 2 in Supply Chain & Warehousing, as well as their LGV C+E (Class 1) Licences.
Most recently, Bradley Jones took on the role of Business Administration Apprentice, after previously working for Christeyns on a temporary contract in the Powder Production department. Bradley’s apprenticeship will run for two years and include studying for a Level 3 qualification in Business Administration.
The four new apprentices join Chemical Engineering apprentice Harry Coop, now in his second year of studying at Bradford University to achieve a BSc (Honours) in Chemistry, and Hena Arif, a QHSE Technician, who will study a Level 3 Health, Safety and Environmental qualification in 2022.
At the chemical manufacturing specialist, apprenticeships are very much a part of the business structure and play a crucial role in taking the company forward. “Our apprenticeship scheme is key for succession planning, identifying and growing talent to fill leadership and business-critical positions in the future. This helps to keep the business at the top of its game,” states HR Manager Sarah Stringer.
Providing young people with the right skills and opportunities is vital for the future prosperity of both Christeyns and the industry, and the company views its apprenticeship scheme as a crucial part of the recruitment strategy. Christeyns’ goal is to offer permanent roles to all apprentices who go through their scheme.
For further information visit: